关键词:渣油加氢 固定床 发泡 结垢 热点 原料
固定床渣油加氢具有工艺成熟、装置运行成本低、可靠程度高的优势,近十年来已是炼油厂处理渣油的有效加工工艺,可为催化裂化装置提供优质的原料。随着新环保法的施行,作为可转化清洁能源的渣油加氢装置还在陆续建设。某炼油厂在全国环保要求越来越苛刻的环境下实行油品质量升级改造,1号渣油加氢装置(下文均用1号渣加表示)于2012年10月建成投产,取得了良好的经济效益和社会效益, 2号渣油加氢装置(下文均用2号渣加表示)也于2017年8月顺利投产。由于对设计意图和操作理念没有完全理解,装置均有一些共同的难点影响其平稳运行,主要有:①热、冷高分界液位分离紊乱(发泡现象),影响高分和低分系统的平稳运行;②混合原料/反应产物换热器E102结垢严重,影响装置的长周期运行;③反应器热点的出现,影响装置的安全运行;④原料的变化,过滤器冲洗频繁,影响装置的满负荷运行。针对上述问题,总结了近几年的操作经验,希望给同行以借鉴。
1、渣油加氢装置的工艺特点
渣油加氢是在一定的温度、压力、氢油比和空速条件下,借助加氢精制催化剂的作用,将渣油中的杂质(即硫、氮、氧和重金属等)转化为相应的烃类和易于除去的H2S,NH3和H2O,金属则截留在催化剂床层中,同时烯烃、芳烃得到饱和,从而得到安定性、燃烧性都较好的优质产品。在处理过程中,原料的平均相对分子质量及烃类分子的骨架结构只有极小的变化,所使用的催化剂为单功能催化剂。
两套装置以减压渣油、直馏轻重蜡油为原料,流程相同,反应部分采用热高分工艺流程,分馏部分采用汽提塔+分馏塔流程。
2、影响平稳运行的因素及应对措施2.1 热、冷高分界液位分离系统紊乱及应对措施
热、冷高分界液面控制平稳是渣油加氢生产操作中的重点。界液位控制不稳影响装置的平稳运行,如热高分液面控制太低,容易将气体带入热低分系统,造成“高压串低压”事故;冷高分液面高可能将油品带入循环氢脱硫系统,严重影响循环氢机的运行,冷高分界面过低会使酸性水脱气罐中串入油、气。
操作现象:DCS画面上热高分V103液位下降或呈锯齿波动,高压空冷A101负荷增大,进入冷高分V105油、水量增大,V105液位上升;因V105液位控制为自控,阀位开度波动增大。现场检查热高分V103磁浮子发生上下大幅波动。冷高分V105界位失灵,玻璃板液面计界位波动,酸性水浑浊,夹杂气泡(简称发泡现象)。
热高分V103发泡现象使部分较重的加氢油品随气相带出,导致后续流程中油水分离不清。理想情况下,油气混合物进入V103上部后,气、液相快速分离。而实际情况是,气相总是带液,液体表面张力大小是携带液量大小的因素,且成正比关系。提高温度可降低胶体的表面张力,表面张力同时受原料性质的影响。渣油中的沥青质在反应过程中容易聚集和沉淀,其结构最复杂也最难分析,沥青质的聚集和沉淀导致液体的表面张力增大,加快换热器结垢。在渣油加氢装置操作中,为了防止沉淀析出,需要维持良好的溶质(沥青质)/溶剂(芳烃油)状态,保持胶体相对平衡。有研究表明:渣油加氢前后沥青质的芳核堆砌表现出明显的长程无序、局部有序的特征,加氢处理后的沥青质芳核易于堆砌,出现多层堆砌、长程有序的类石墨结构[1]。沥青质结构中出现较大的芳香核,沥青质群岛型结构有向大陆型结构转化的趋势[2]。因沥青质在饱和环境下更容易聚集,且加工低硫原油时渣油大分子更难转化[3],加工石蜡基原油(如拉帕/卢拉)和高沥青质原油(如巴士拉)的混合原油时,沥青质更容易聚集,更易诱发热高分的分离问题(如热、冷高分发泡问题)。为防止沥青质聚集/析出导致的发泡,尽量避免加工石蜡基(如拉帕/卢拉)和高沥青质(如巴士拉)的混合原油[4]。
经过对1号渣加4个周期和2号渣加1个周期的运行分析,发泡现象一般发生在装置开工初期1~3月的时间。引起V103发泡的主要因素有以下几点。
(1)气体量过大。开工初期催化剂活性较高,裂解气较多是因素之一。另外,2号渣加的设计氢油比为600,设计混合氢流量166 700 m3/h,现实际氢油比为771,混合氢流量为222 650 m3/h,超设计值约55 950 m3/h。加上二反、三反、四反入口的急冷氢量,导致V103入口的实际气体流量更大,更加重了气体的带液情况,装置参数见表1。
表1 两套渣油加氢装置参数对比s
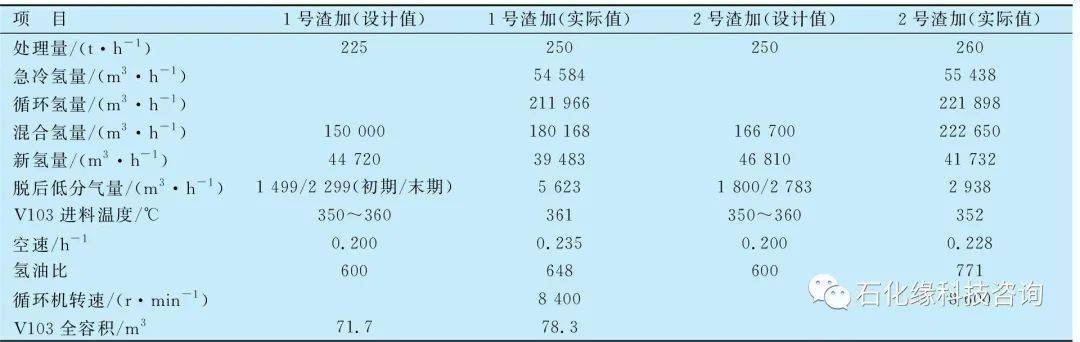
(2)V103气相空间偏小, 气液分离不足,导致出现气体带液。
(3)V103进料温度过低。V103进料温度设计值为350~360 ℃,目前此温度仅在350 ℃左右。进料温度低造成液相黏度增加,表面张力增大,小液滴难以结合成大液滴,造成部分小液滴被气流带出;另一方面,被拉成薄膜的液滴包裹的气体难以析出,加重了液体被带出的趋势[5]。
操作调整:
(1)降低装置加工量和渣油掺炼量,使发泡的状况得到改善,保证装置平稳。
(2)降低循环机转速,使混合氢流量下降,V103进料中气相流量下降,增强V103气液分离效果。
(3)适当提高V103的进料温度,降低胶体的表面张力。
(4)调整加工原料,尽量避免加工沥青质易析出的混合渣油。为争取经济效益最大化,渣油加氢的减压渣油多是含两种或多种原油的混合减压渣油,一定程度上给渣油加氢装置增加了操作难度。
(5)开工初期催化剂活性较高,裂解气较多,应适当控制反应深度,在产品质量合格时,应适当降低反应温度。
2.2 高压换热器E102末期换热温度低
1号渣加换热器E102设计管程为混合原料,入口温度284 ℃,出口温度359 ℃,壳程为反应产物,入口温度425 ℃,出口温度360 ℃,有效传热温差69.9 ℃。随着装置第三周期运行,换热效率下降严重,原料换热后温度逐渐下降:初期混合原料入口温度289 ℃,经E102换热后最高达315 ℃;后期混合原料入口温度296 ℃,经E102换热后只能达到317 ℃左右,低于设计值。由于原料E102换热终温不够,造成加热炉F101入口温度低,加热炉负荷偏高,运行后期催化剂活性降低,反应温度需进一步提高,加热炉难以满足运行要求。
鉴于上述情况,2016年12月更换了E102,换热面积由741 m2增大到1 170 m2,换热温度提高约30 ℃,一定程度上缓解了加热炉负荷过大提温受限的局面,保证了产品质量,但操作末期仍出现了换热效率下降的情况。
每周期换剂期间,对换热器进行检查,发现壳程管束结垢严重,第一周期换热器两壳程密封条脆化严重,存在内漏现象,因此将原321材质密封条更换为哈氏合金。解决了换热器内漏之后,管束外壁结垢可能是传热效率下降的主要原因。垢物经化验为沥青质等物,其成因是反应产物温度过高导致胶质、沥青质在管束上沉积,同时介质的流速较低没有起到有效的冲刷作用。
表2为E102的技术参数,2号渣加装置E102为2台串联,缩小壳径,将结垢侧介质改走管程,并提高结垢侧介质流速。目前运行10个月换热器的副线开度在38%,仍能满足要求,而1号渣加装置换热器E102的副线在运行3个月后已完全关闭,典型运行数据见表3。
从表3数据可以看出,2号渣加换热器换热较充分,分析原因如下:
(1)该换热器为纵向挡板分流的两壳程U形管换热器,其传热十分接近于纯逆流换热,根据逆流换热的温度变化与管长的关系,在其他换热条件不变的情况下,足够的管长可以提供足够的换热深度,最终使冷热流体的初、终温在理论上可以无限接近,2号渣加在日常操作中曾出现过反应产物终温仅比进料初温高2 ℃的情况。
表2 E102的技术参数
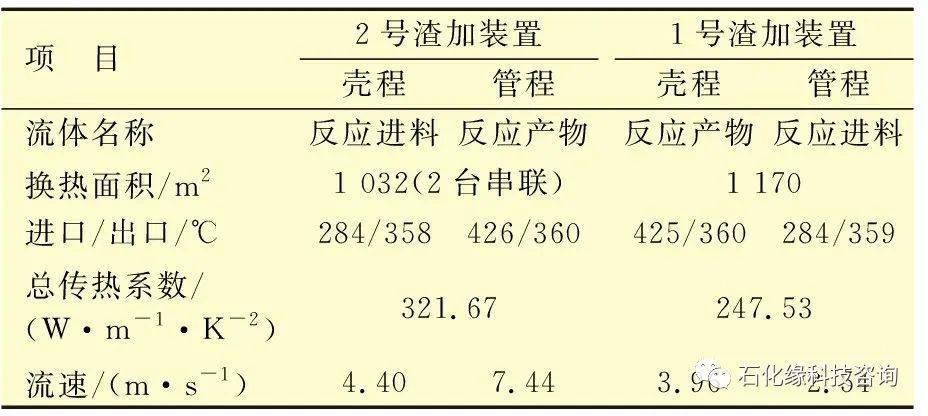
表3 第10个月E102换热情况对比
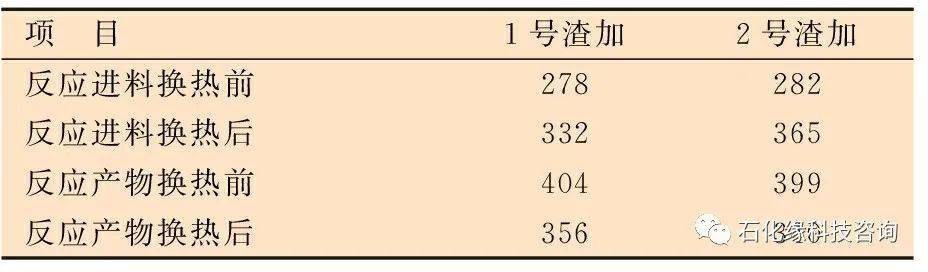
(2)小外径、高流速和易结垢流体走管程的设计有效降低了积垢对于后期操作的影响;此外,高流速也造成了流体处于足够的湍流状态,利于传热。
(3)1号渣加的换热器虽然单台换热面积大,但低流速易积垢,影响传热,而较短的管长又没有提供足够的换热空间,低流速使湍流程度较低,导致传热并不充分。因此1号渣加应在压力降不超过允许限度的情况下,提高流体流速,原设计的管程26 kPa的压力降有待商榷。
(4)换热计算时除必须经过正常的传热计算外,对有关数值的合理性也应加以分析并调整。两套装置E102的换热效果差异应该是设计计算时合理性分析不同所致。
操作及设计上的应对措施:
(1)在线速度一定的条件下,通过调整操作,控制反应温度,减少胶质、沥青质形成。
(2)1号渣加的E102的管壳程物料互调,见表3。将反应产物改走管程,提高速度,对沉积物起到冲刷作用,虽然1号渣加E102面积增大了,流速没有增大,效果不理想,如参照2号渣加的改造方式可能效果更佳。
2.3 反应器部分热点的出现及应对措施
渣油加氢反应器制约装置安全长周期运行,有两个原因:一是催化剂性能无法使产品质量合格,二是反应器床层压力降达到设计值或出现无法控制或预测的热点,运行无法继续。出现热点时,需综合判断,优化反应器内的催化剂装填,以及平衡每个反应器的床层平均反应温度BAT对降低反应器的压力降以及出现热点的风险非常关键。
反应器内催化剂径向装填不均,将可能导致反应物料在催化剂床层内“沟流”、“贴壁”等走“短路”现象的发生,也可能导致部分床层塌陷,一旦催化剂床层径向疏密不均,床层内存在阻力差异,气液相分离就易形成热点。热点一旦出现,该区域催化剂结焦速度将加快,床层压力降增大,反过来又导致流经该区域的气相减少,反应热量集聚,进一步推升该区域温度,形成恶性循环[6]。这样一来,高温热点的出现一方面影响了装置的安全,另一方面缩短了装置的运行周期。
优化催化剂级配装填过程来控制反应器的温度分布可以提高催化剂的利用率,同时也能减少热点和压力降问题的出现,同时操作平稳、积炭和金属沉积分布均匀是反应器压力降稳定的保障。
1号渣加装置第1、第4周期均出现热点。第1周期运行420 d时,一反R101出现热点,温度达432 ℃,通过降低掺渣量和入口温度后,上升速度趋于缓慢,但仍至484 ℃。后期生产中再次提高掺渣量和入口温度,热点温度上升速度仍较快。第4周期运行400 d时一反出现热点,由394 ℃逐渐上升,第404 d达最高点728 ℃后又逐渐下降,第411 d的温度下降并保持在383 ℃,判断为该热偶点周围已结焦。
反应器床层热点的形成有本身固有且不可调整的因素:
(1)反应器入口分配器的设计、制造和安装均有可能导致液流分配不均形成热点;
(2)催化剂装填径向疏密不均形成的热点。
操作因素有:
(1)低负荷运转导致床层液流分布不均,局部形成热点,热量不易带走,从而热点逐渐扩大;
(2)原料油性质变化,杂质过多,导致大量杂质截留在催化剂床层,堵塞催化剂孔道;或因黏度过大导致液流分布不均,形成热点。
对于不可调整的因素可选择合适的分配盘,避免物流分布不均产生局部热点;另外,选择负责任的装剂公司并全程跟踪监控以提高装填质量。
应对热点的措施主要是调整操作:
(1)提高循环机转速以提高循环量,带走反应床层热量;
(2)降低反应器入口温度,从而降低整个床层的温度,控制热点上升的速度;
(3)调整原料结构,优化原料性质,尽量满负荷生产,避免低负荷出现的偏流,如负荷受限可改部分精制常渣循环;
(4)密切关注反应器壁温以及该反应器床层压力降,如靠近热点的壁温有所变化立即启动紧急停工预案,如床层压力降上升较快说明热点周围结焦增大,达到设计压力降时启动停工程序。实际运行中,热点温度先涨后降,并未影响压力降和器壁温度。
2.4 原料的变化及过滤器冲洗频繁
对于固定床反应器而言,控制床层压力降,减少催化剂结焦是装置长周期运行的关键。在导致床层压力降上升的若干因素中,原料中含有机械杂质是主要因素。
装置正常生产时,减压渣油进料来源有两路:罐供渣油和直供渣油。罐供渣油在罐区有一定的沉降时间,避免了过多的杂质带入装置,原料过滤器工况稳定,对正常生产影响较小;而直供渣油流量及杂质含量变化频繁,可能会造成原料过滤器反冲洗频繁,过滤器压差大幅变化甚至超出正常的控制范围。为保证催化剂使用寿命和装置的长周期运行,装置被迫降低处理量和掺渣量,影响了装置的正常平稳生产,也降低了装置的经济效益。
应对措施:加强原料管理,减少原料切换,如有条件尽量提高原料的温度以降低黏度,缓解过滤器的频繁冲洗问题。如过滤器冲洗频繁严重影响正常生产,则将滤芯抽出清洗后投用。
3、总 结
渣油加氢装置在国内经过十多年的发展运行,目前仍是重油清洁化最重要的加工工艺。渣油加氢装置的操作及设计理念仍有进一步优化的空间,随着大家对渣油加氢装置认识加深,设计意图及操作理念进一步明确,装置设计将更加合理,操作更加便捷。通过对现运行的渣油加氢装置的分析,可以探索出一套应对影响装置平稳运行问题的操作调整方法及措施。
(1)通过降量、提温、调整原料等措施可一定程度上缓解发泡的现象,但应结合目前装置出现的问题,对发泡物料的性质及成因做进一步分析,同时优化催化剂级配,从反应条件上降低开工初期出现的发泡风险;也需考虑适当增大气相空间或增设强化气液分离的内件,使装置能够长周期稳定运转。
(2)换热器换热效率的下降影响反应温度,虽然各个厂家通过增大换热面积缓解了这一问题,但依然未从根本上解决。目前从表观上看反应产物改走管程效果较好,提高高温段易结垢侧介质的线速度是减缓沥青质在管束上结垢的最有效手段。同时研究单位应提供换热器两侧介质的稳定性分析数据,以便更好地指导设计选型。
(3)为减少热点温度的出现,应尽量避免负荷过低,生产上可通过降低反应器入口温度加以解决,并制定应急预案。
(4)过滤器冲洗周期的延长主要靠原料的管控以及尽量提高原料的温度,使渣加装置满负荷运行,提高装置的运行经济效益。